SWM - Structural and Materials Mechanics
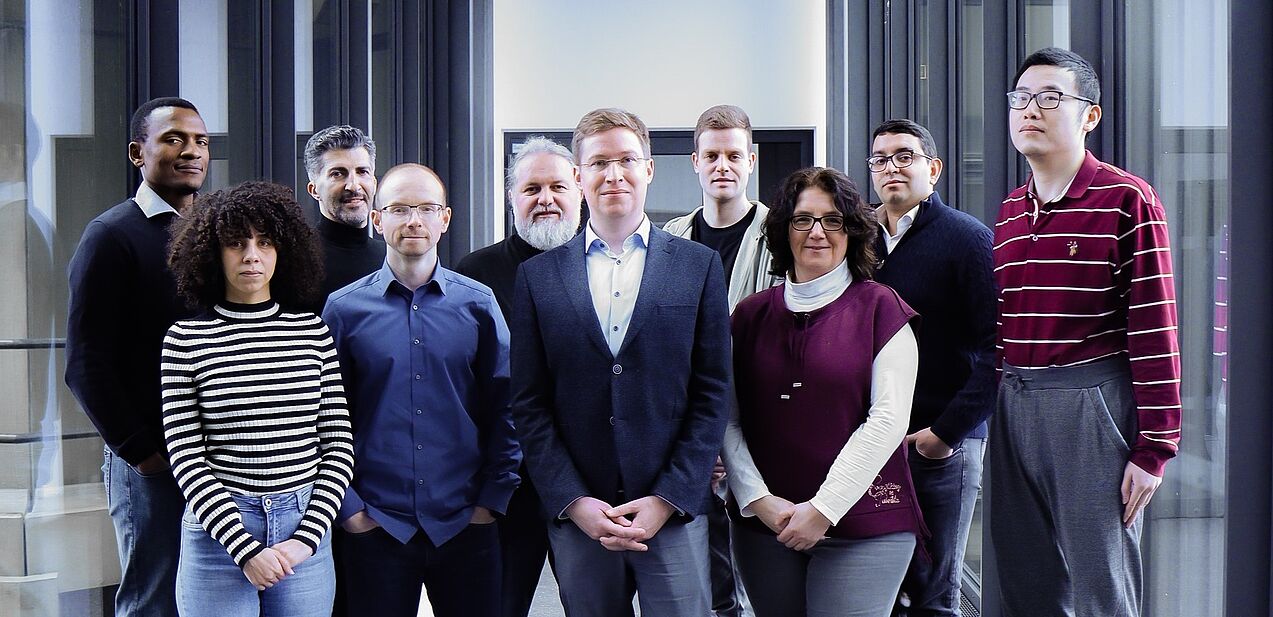
The development and manufacture of innovative products using new materials requires in-depth knowledge of analytical and numerical calculation methods for the safe design of components and machines. Imparting this knowledge is one of the main tasks of the Chair of Structural and Materials Mechanics in the Bachelor's and Master's degree programmes. The combination of training, modelling, experiment and application at SWM prepares future engineers in several layers for the ever-increasing challenges in the calculation of mechanical engineering components in industry.
Read more on the page of the department.
Methodological expertise
-
Multiaxial tests
-
Cyclic tests
-
Inductively controlled temperature tests
-
Optical 3D measurement technology (GOM Aramis / Atos)
-
FEM simulation (Abaqus)
-
Material modelling and finite element development
-
Parameter identification (homogeneous + inhomogeneous)
-
Implementation of material laws in the commercial FE software Abaqus (UMAT, UEL)
-
AI-supported material modelling (ANN, PINN)
Subject areas
Experimental investigations
-
Uniaxial tests (tension/compression)
-
Biaxial tests
-
Axial-torsional tests
-
Experimental tests on inductively heated components
-
Cyclic tensile tests with optical extensometer (also strain-controlled)
-
Optical component and deformation measurement (DIC multisensor)
Modelling
-
Damage modelling with regularisation
-
Model and mesh adaptivity of multi-scale problems
-
Optimal model and test planning
-
Phase field modelling of high-temperature components
-
Phase transformation plasticity
-
Multiscale modelling of heterogeneous material systems such as multilayer tool coatings
-
Anisotropic hardening behaviour of polymers
-
Adhesive layer failure with stochastic methods
-
Curing of epoxy resin based materials
Parameter identification
-
Parameter identification of non-linear materials using optical methods
-
Parameter identification with fuzzy and stochastic methods
-
Parameter identification with epistemic and aleatory methods
Simulation
-
Adaptive mesh refinement for parameter identification and phase field simulation
-
Simulation of manufacturing processes taking phase transformations into account
-
Simulation of anisotropic plastics as a result of the stretching process
-
Simulation of inelastic adhesive layers and fibre-reinforced plastics in lightweight automotive construction
-
Development of numerical methods for the efficient simulation of finite element structures
-
Moulding simulation of uncured prepregs
-
Curing simulation of epoxy resins