Everything under one umbrella
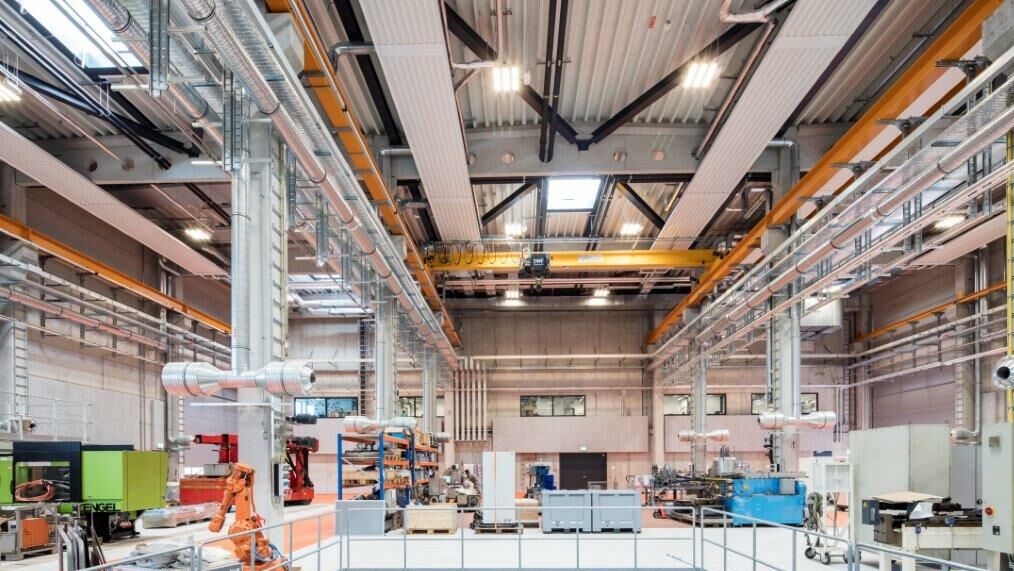
The technical centre within the lightweight research building offers state-of-the-art equipment for the production and testing of components in around 2000 square metres of space.
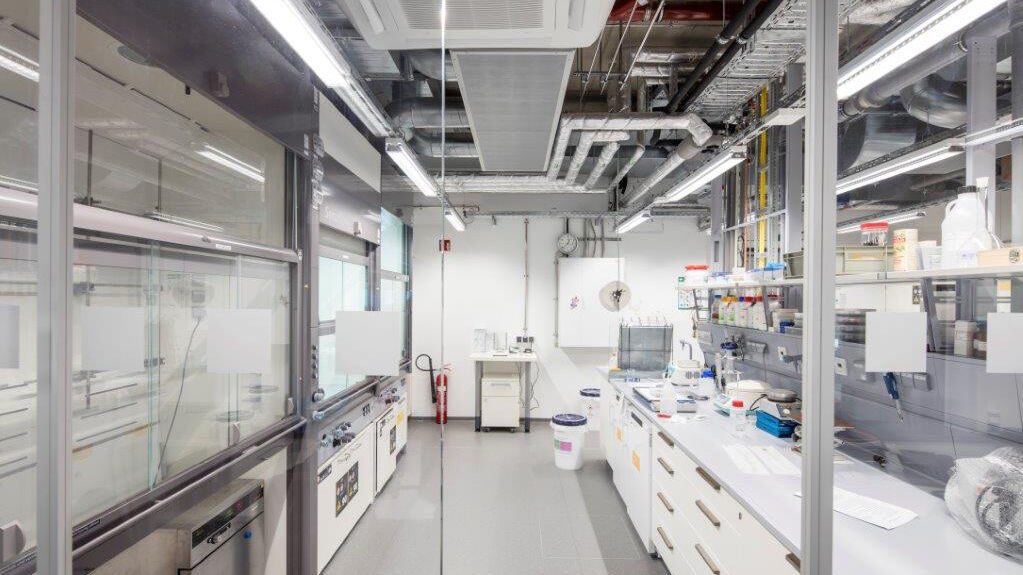
In the immediate vicinity, with visual contact to the technical hall, is the laboratory area for electrochemical tests, hardness tests and chemical synthesis. The adjacent analytical laboratories are equipped with modern devices for nanostructuring, microscopy and spectroscopy as well as characterisation.
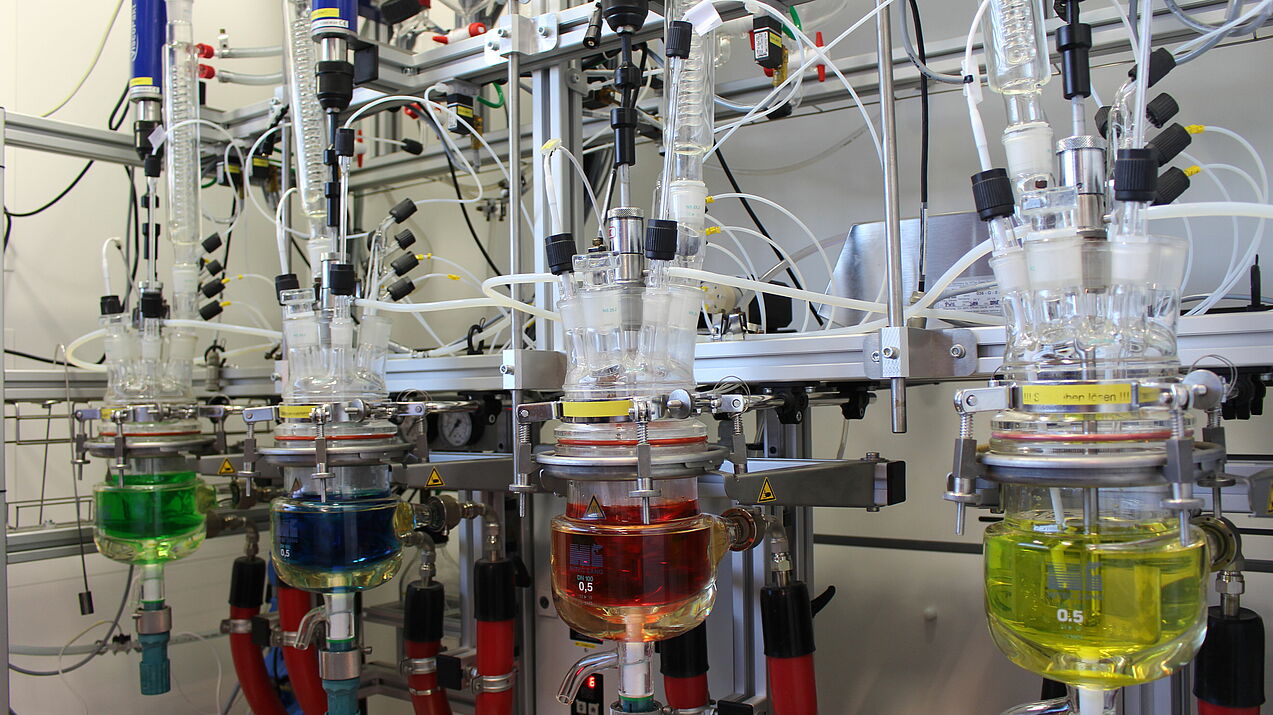
The ILH building houses the laboratories of the Coatings, Materials & Polymers Division. Here you can find information about their equipment. The contact person is Manuel Traut.
Dr. Christoph Ebbert is our contact for the equipment for surface analysis of technical and macromolecular chemistry.
- ILH parallel reactor
- Batch synthesis reactors for polymerisation reactions (various sizes, 1 kg / 4.5 kg / 30 kg)
- Freeze-drying system
- SLA 3D printer for UV resins
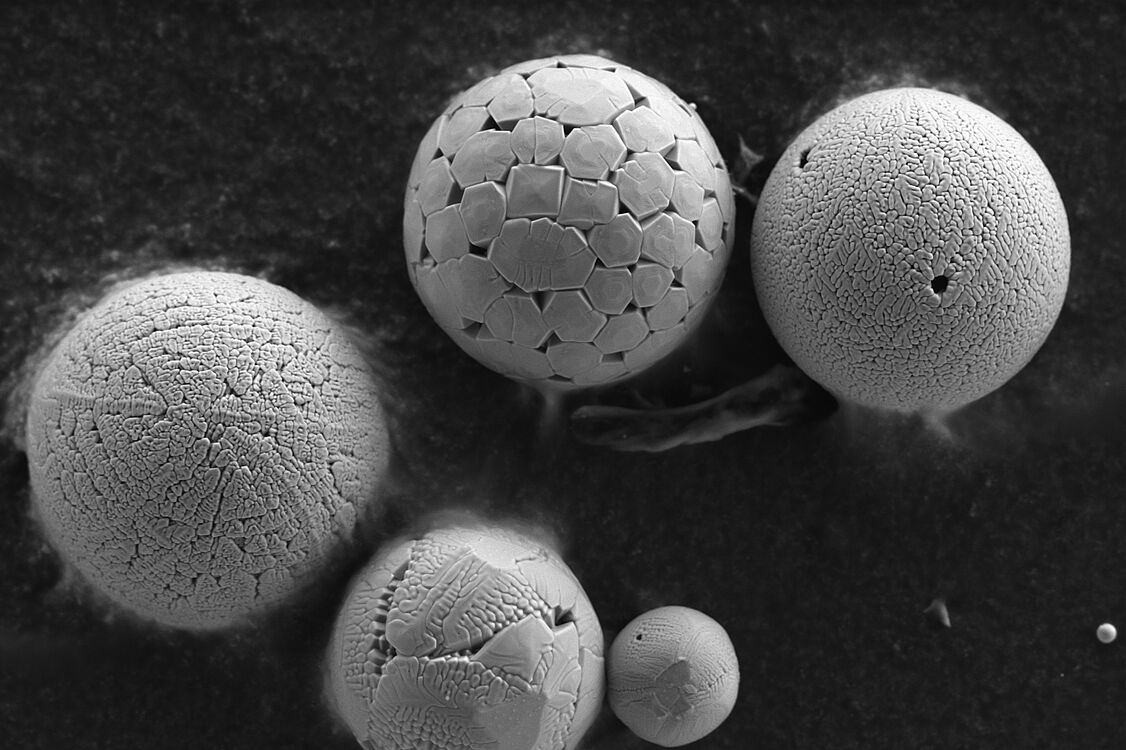
This field includes processes for self-assembled nanostructuring and surface characterisation as well as scanning and transmission electron microscopy for high-resolution imaging and analytics.
- Nanostructuring squeegee
- Tensiometer K100SF (Krüss company)
- Drop Shape Analyzer DSA25E (Krüss Company)
- JEOL JEM-ARM200F
- Jeol JSM-6300F SEM
Contact person:
Nanostructuring squeegee
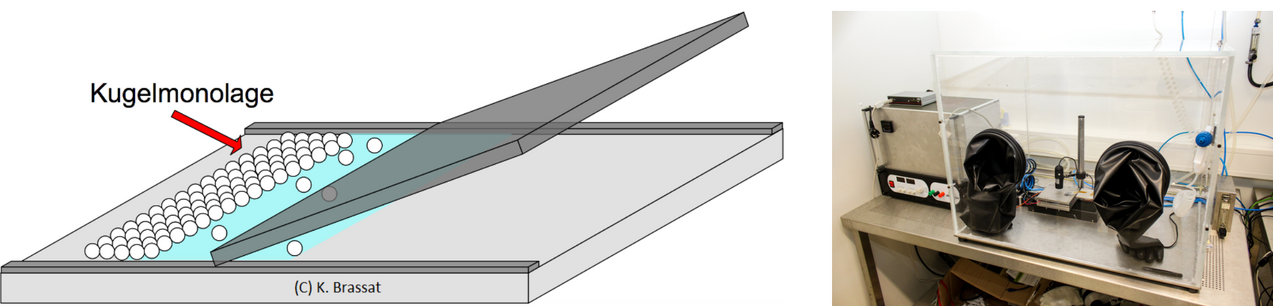
Fabrication of self-assembled colloidal nanospheres masks on solid surfaces by agitation of a droplet.
Squeegee apparatus:
- Mobile substrate holder
- Peltier sample table with adjustable temperature
- Plexiglas glove box with dry gas inlet
- Temperature and humidity monitoring
- Adjustable tilt angle of the squeegee plate
- In-situ observation with light microscope
- Computerised control
Tensiometer K100SF
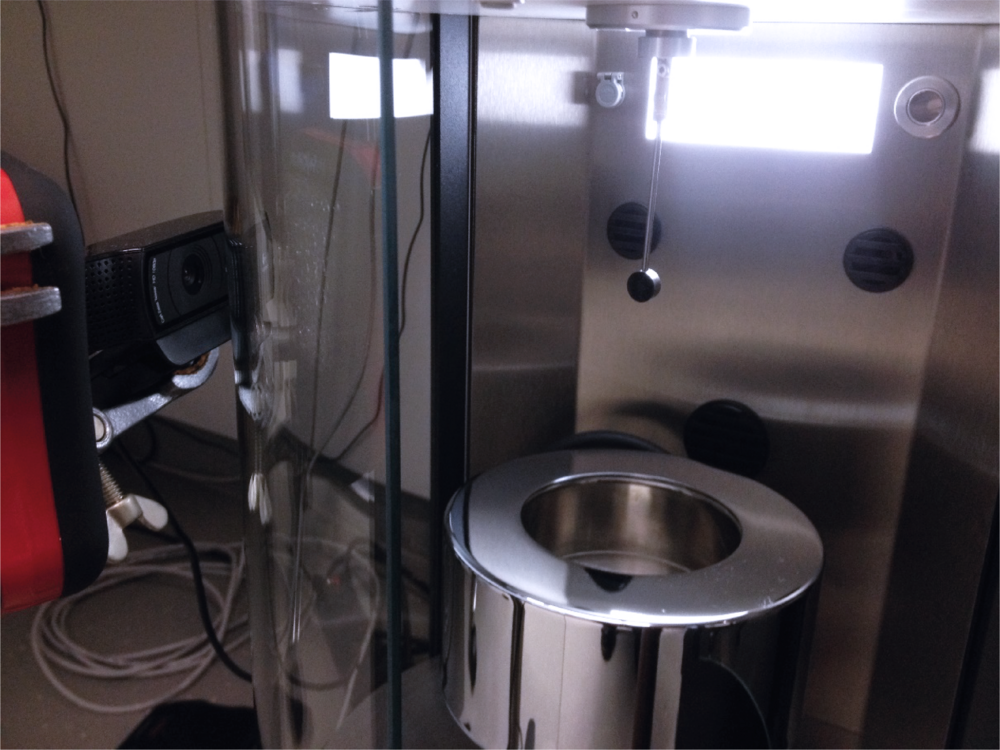
Contact angle measurement on single fibres to analyse wettability.
- Weight measurement: up to 3 g, resolution 0.1 µg
- Sample stage position: range of motion 110 mm, resolution 0.1 µm, speed 0.09 - 500 mm/min
Drop Shape Analyzer DSA25E
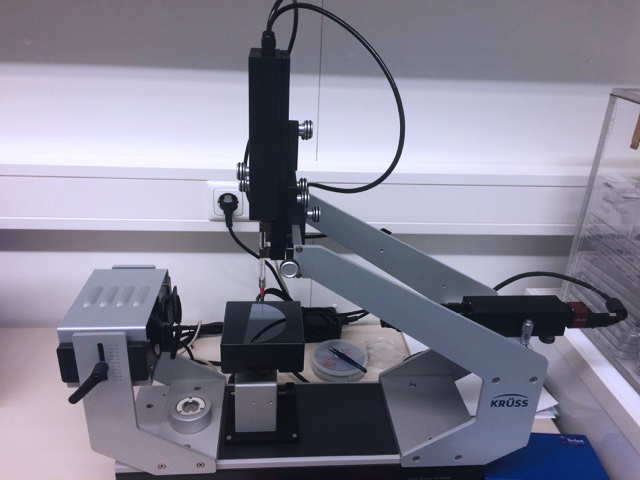
Optical measurement of static and dynamic contact angles on solid surfaces (method of the resting drop), determination of solid surface energies and surface tensions of liquids (method of the hanging drop).
- Lifting table (z-axis)
- Software-controlled double dosing unit
- Zoom lens, camera (resolution 656x492 px)
Transmission electron microscopy
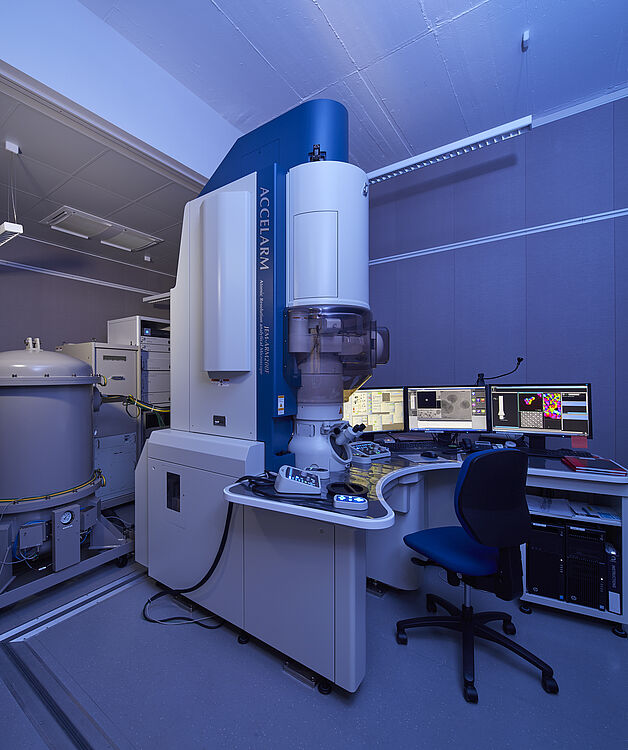
This field includes methods for self-assembled nanostructuring and surface characterisation as well as scanning and transmission electron microscopy for high-resolution imaging and analytics.
JEOL JEM-ARM200F: Cs-corrected ultrahigh-resolution field emission TEM/STEM
- Accelerating voltage: 30 - 200 kV
- Cold field emission source
- Illumination-side Cs corrector with aberration correction up to 5th order (CEOS ASCOR)
- TEM point resolution: 0.19 nm, information limit: 0.11 nm
- STEM point resolution: 0.08 nm at 200 kV, ≤ 0.20 nm at 30 kV
- Energy resolution ≤ 0.30 eV (FWHM ZLP)
- 4k x 4k CMOS camera (Gatan OneView)
- 2k x 2k CCD camera (Gatan UltraScan)
- STEM BF, ABF, DF and HAADF detectors
- 8-fold segmented STEM DF detector for differential phase contrast imaging
- Energy dispersive X-ray spectroscopy system with SDD detector (JEOL)
- Post-column energy filter for EELS, Dual-EELS and EFTEM (Gatan GIF Quantum ER)
- Single-tilt, wide-angle and analytical double-tilt sample holder
Jeol JEM-2000FX
- Accelerating voltage: 80 - 200 kV
- Thermionic electron source (currently tungsten)
- Point resolution ~0.3 nm
- Sample holder: single tilt holder, 2 samples, max. tilt +/- 30°.
- Energy dispersive X-ray spectroscopy system: EDAX with Be window
- FastScan CCD camera (TVIPS)
Jeol JSM-6300F SEM
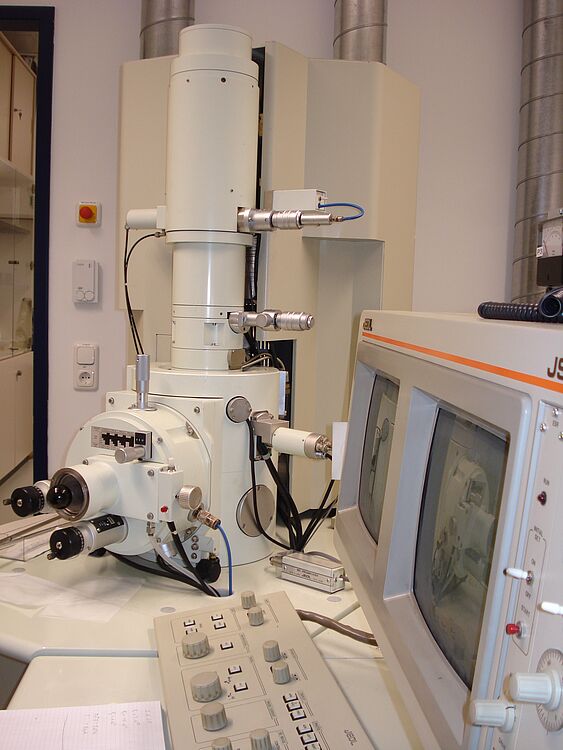
- FEG emitter
- Accelerating voltage: 0.2 - 30 kV
- Detectors for secondary electrons and backscattered electrons
- Point-electronic grid control and data acquisition unit
Extrusions- und Spritzgießanlagen befinden sich derzeit in den Laboren der Kunststofftechnik Paderborn.
Kontakt:
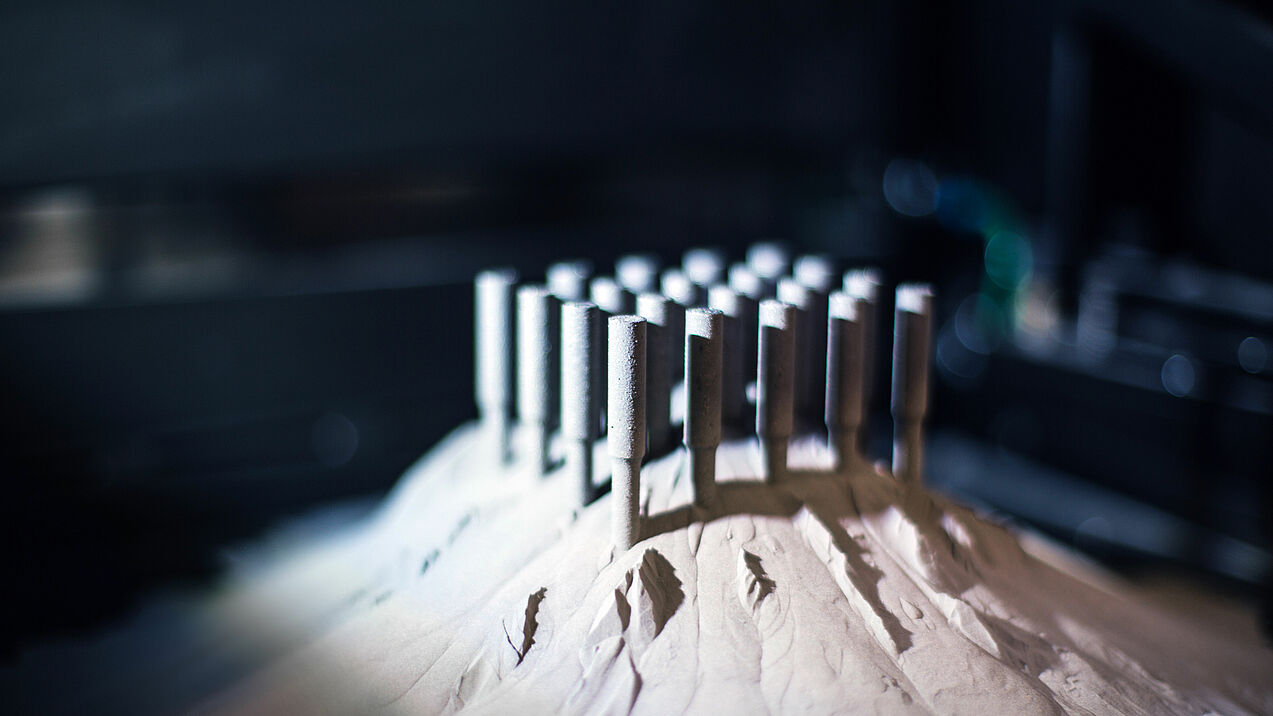
We have various systems for additive manufacturing. Different SLM systems and a laser build-up welding system are used.
- Laser beam melting system LASERTEC 12 SLM (400 W)
- Laser melting system LASERTEC 30 SLM (600 W /1000 W)
- Laser build-up welding system LASERTEC 65 3D
Contact person:
LASERTEC 12 SLM
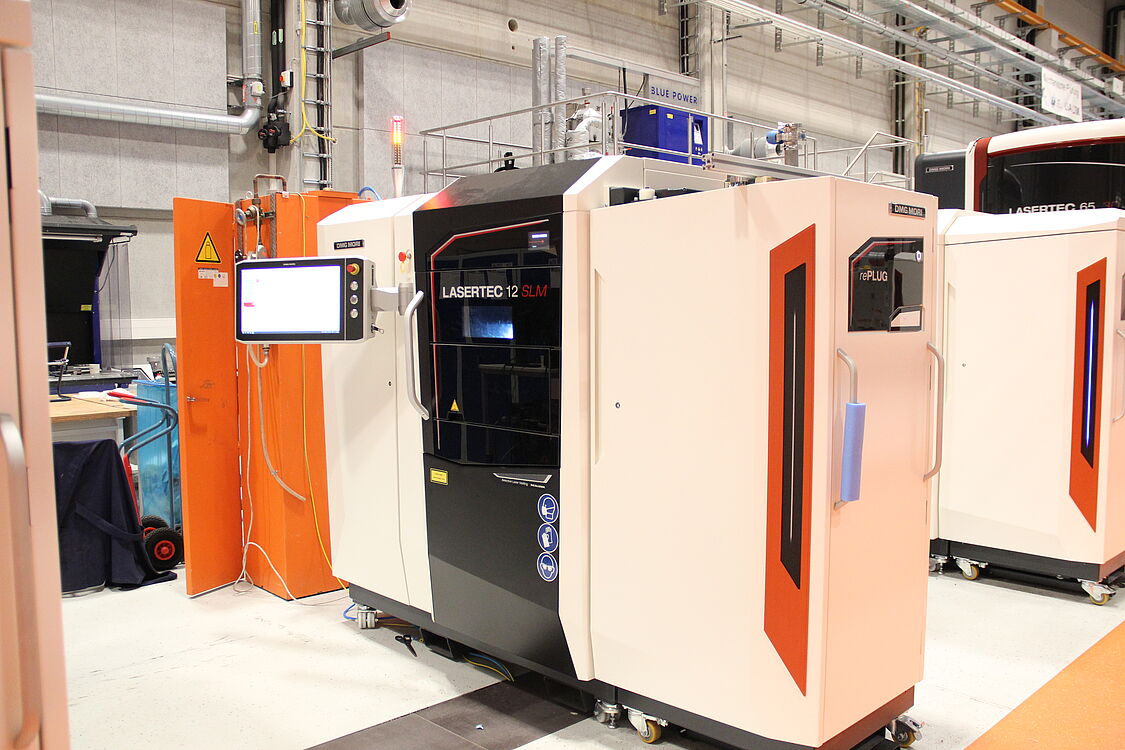
Construction volume X | 125 mm |
Construction volume Y | 125 mm |
Construction volume Z | 200 mm |
Min. layer thickness | 20 µm |
Min. focus diameter | 35 µm |
Laser power standard | 200 W / 400 W |
The aim of the metal process chain is to map various process routes for the production of sheet metal components in the technical center and thus achieve a high degree of automation. This primarily involves the preparation of semi-finished products through mechanical, thermal or chemical pre-treatment, which can then be formed in the presses or further processed in separate test benches.
Some process routes can thus be fully mapped in the process chain, while others are used to supply the large press functional area.
We have various facilities for metal processing. These include presses and a hardening furnace.
- Hydraulic drawing press DHC-1000/600 (Schuler)
Contact person: Dr.-Ing. Tim Rostek
We have other smaller presses, the contact is here: Moritz Ostermann
Schuler Press: DHC-1000/600-3.0x2.0
Technical specifications
- Nominal force 10,000 KN
- Pulling ram force 6,000 KN
- Max. Sheet holder force 4,000 KN
- Control via programmable logic controller (PLC)
- System: Siemens Simatic S7-15xx F
- Programming software: Step 7 TIA Portal
- Swivelling suspension desk
Application
- Guiding or picking up complex tool systems. Defined traverse movement, fine resolution proportional adjustable pressure setting and powerful press or process control. Forming of sheet metal.
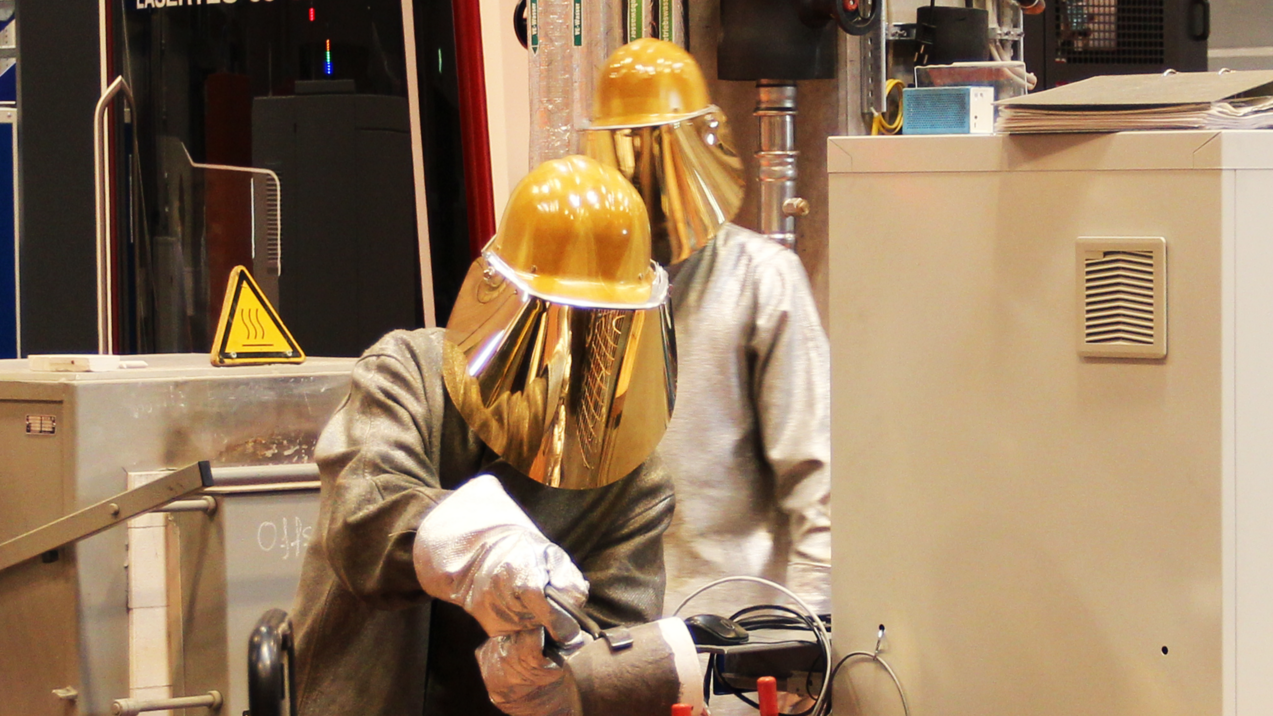
Wir verfügen über verschiedene Anlagen zur Herstellung und Vorbereitung von Bauteilen. Dazu gehören eine 2-Rollen-Gießwalzenanlage, ein 3-Achsen-Hybrid-Markierlaser und verschiedene Öfen.
Weitere Informationen finden Sie auf der Seite der Fachgruppe Werkstoffkunde (LWK).
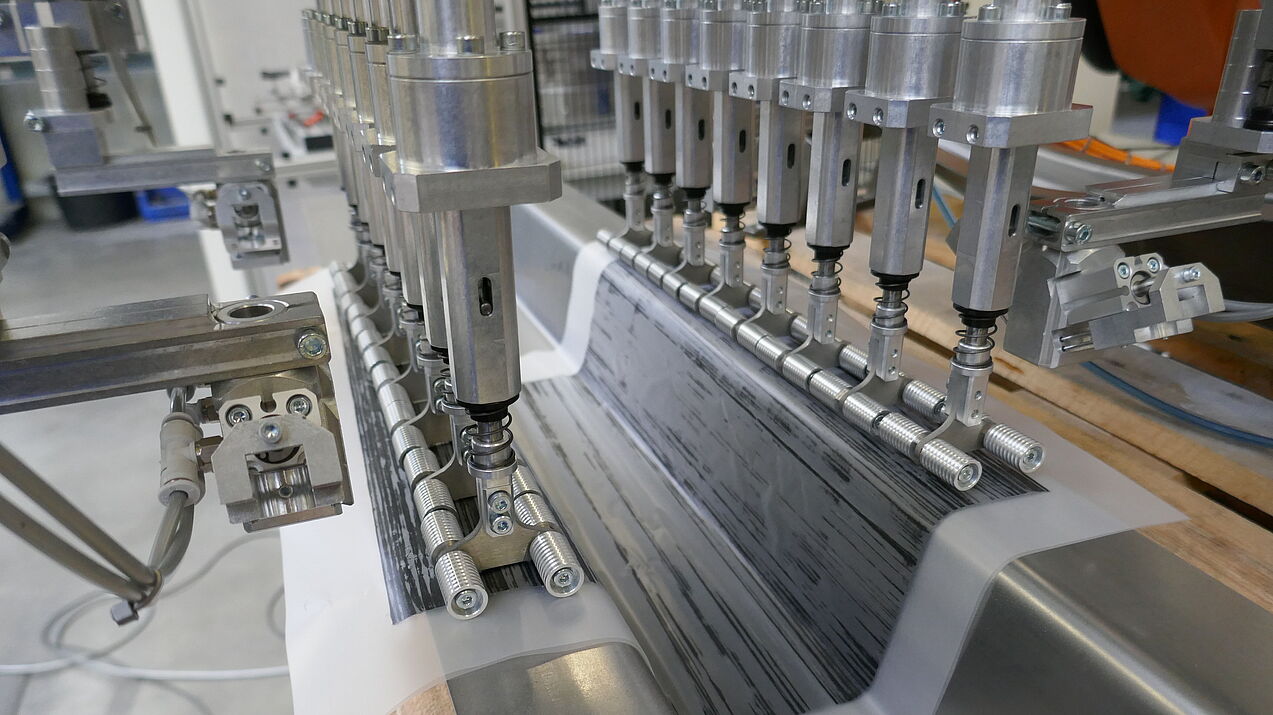
We have various facilities that are required for semi-finished product production and preparation as well as for component production. This includes a gantry cutting system for automatic cutting as well as prepreg, resin injection systems and hydraulic presses.
Semi-finished product production & preparation
- Portal cutting system for automatic cutting
- Prepreg plant BaseCoater BC 46
Semi-finished product processing & component production
- Resin injection plant Tartler GmbH
- Resin injection plant Wolfangel GmbH
- Hydraulic press LaboPress P200S Vogt
- Servo motorised screw press Synchropress GmbH
- Hydraulic press Hessmert
Contact person: Maximilian Kaiser
Portal cutting system: CAMTEC AUTOMASK Vario
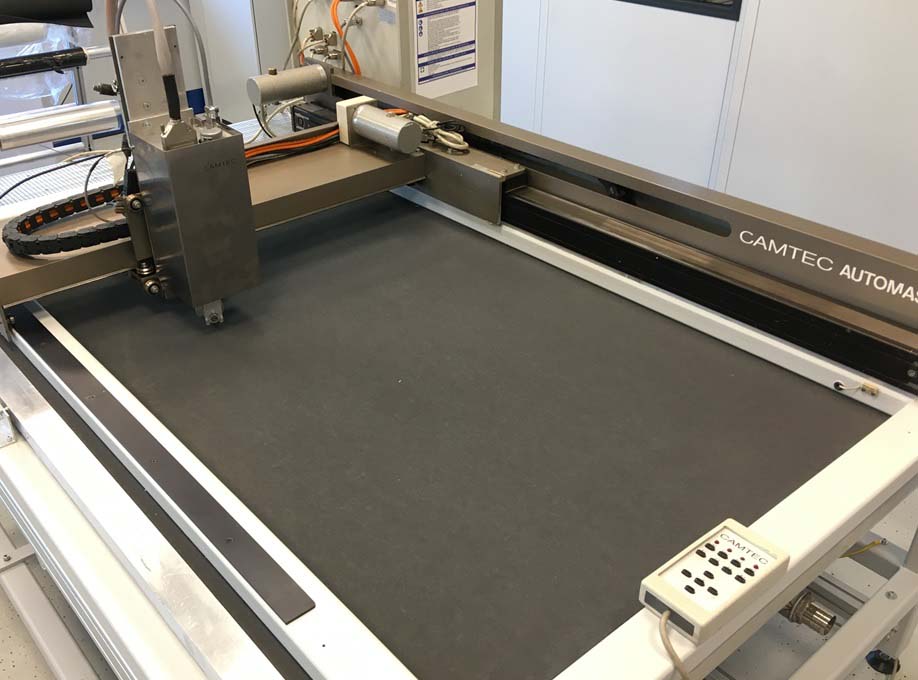
Technical specifications:
- Manual / Automatic trimming
- Tangentially guided, rotating knife
- Working area: 1,000 mm x 580 mm
- HPGL interface (conversion from e.g. DXF format possible)
- Vacuum table for secure fixing of the material to be cut
Application:
The CAMTEC AUTOMASK Vario gantry cutting machine is used for cutting flat templates as well as dry or pre-impregnated semi-finished fibre products.
Prepreg system: BaseCoater BC 46 (Coatema Coating Machinery GmbH)
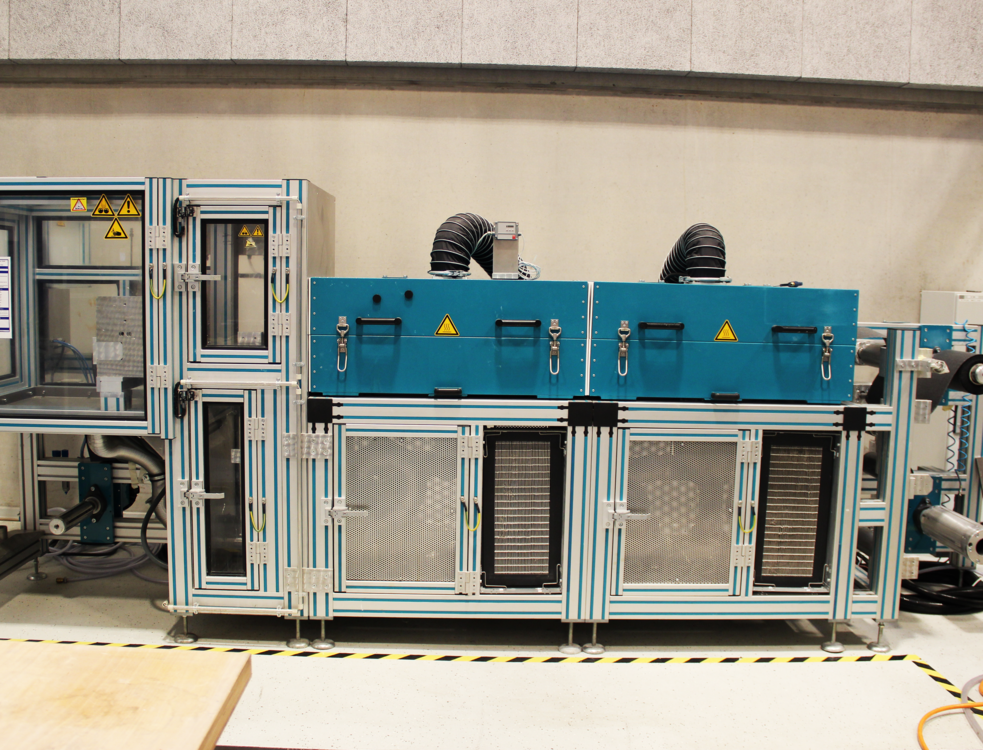
Technical specifications:
- Working width / roller width: 250 mm /300 mm
- Speed: 0,1 - 2 m/min
- Tractive force: 25 - 250 N
- Hot air drying at max. 235°C
- Coating tank volume: 1 litre
Application:
Automated coating machine for the production of pre-impregnated fibre matrix semi-finished products (prepregs). The prepreg production process consists of unwinding, coating, heat treatment (drying and cooling) and winding.
Resin injection plant Tartler GmbH
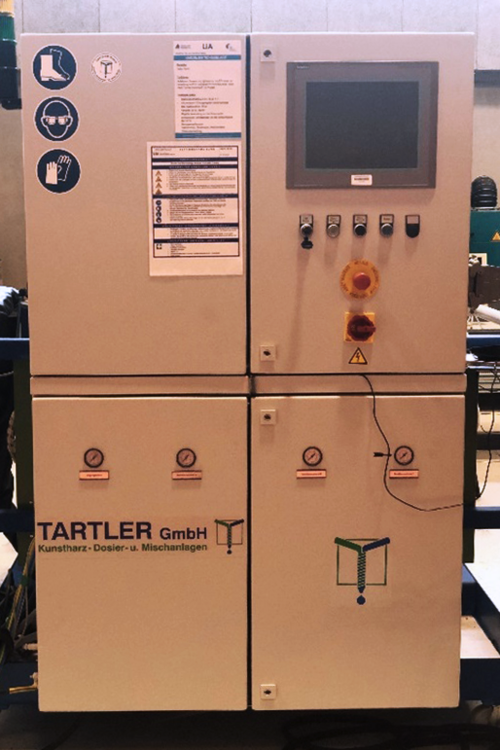
Technical specifications:
- Processing of up to three components
- Mixing ratios A:B:C up to 1:1:1
- Volume flow / pressure controlled injection process
- Max. Injection pressure: 60 bar
- Material throughput: up to 1 kg/min
- Heating of storage tanks and hose package up to 130 °C
- Measuring systems/sensors: injection pressure, temperatures, mixing ratio
- Process monitoring
Application:
Preheating, dosing and injection of EP or PU resins for the production of FRP or FRP-metal hybrid components by means of a (vacuum-assisted) resin injection process (resin transfer moulding, RTM).
Wolfangel GmbH resin injection plant
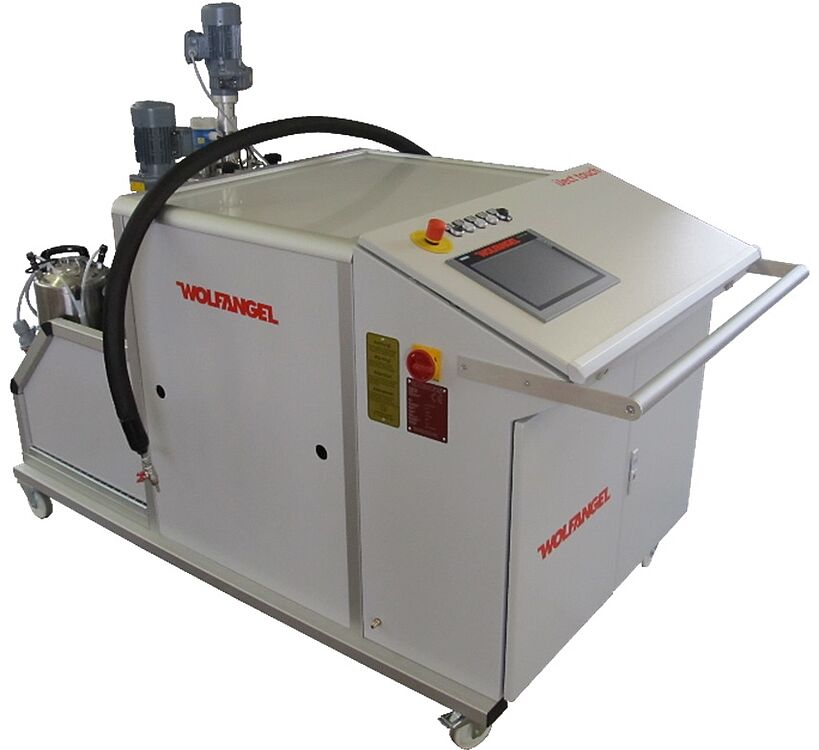
Technical specification:
- Processing of up to three components
- Mixing ratios A:B:C up to 1:1:1
- Pressure-controlled injection process
- Max. Injection pressure: 40 bar
- Material throughput: up to 500 g/min
- Heating of storage tanks and hose package
up to 120 °C - Measuring systems/sensors: injection pressure, temperatures, metering ratios
Application:
Preheating, dosing and injection of EP or PU resins for the production of FRP or FRP-metal hybrid components by means of a (vacuum-assisted) resin injection process (resin transfer moulding, RTM).
Hydraulic press: LaboPress P200S (Vogt Labormaschinen)
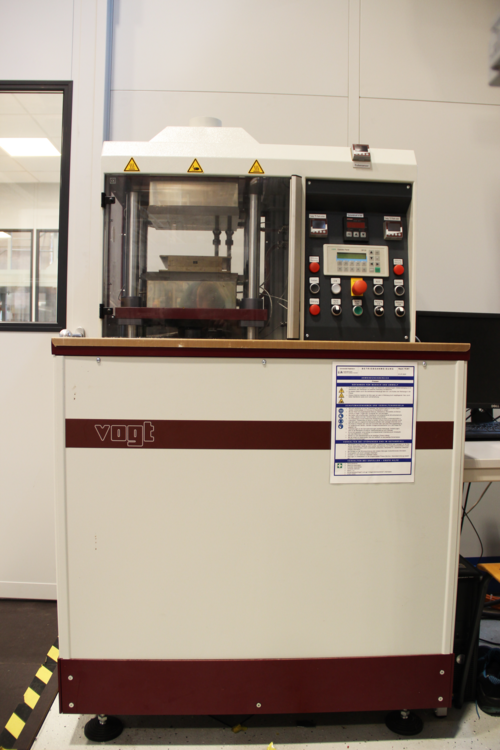
Technical specifications:
- Pressing force infinitely variable (SPS control).
- Pressing force: 1.2-24.5 kN
- Tool plates heatable up to 300 °C
- Cooling of tool plates by means of water/compressed air mixture
- Working area: 200 mm x 200 mm
- Installation height: 175 mm
- Lifting speed: 20 mm/sec (fast speed), 0.5 mm/sec (creep speed)
Application:
The LaboPress P200S is an all-rounder suitable for a wide range of tasks and laboratory applications. Temperature and force control make it suitable for the repeatable production of samples and smaller components, e.g. by means of prepreg pressing.
Servo motorised screw press (Synchropress GmbH)
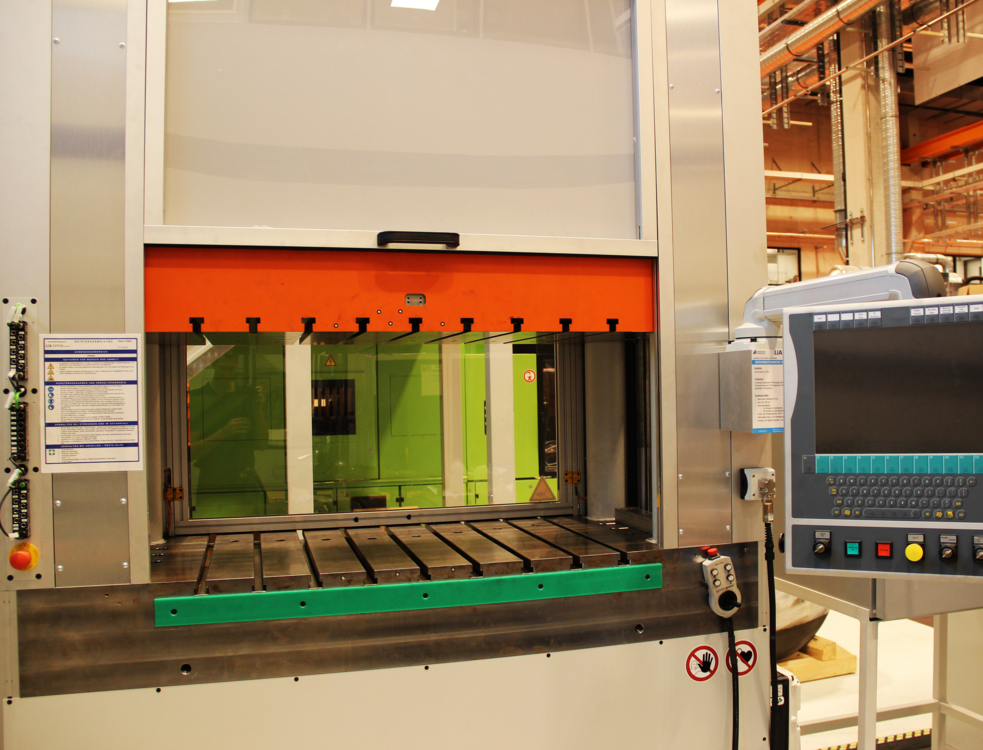
Technical specifications:
- Maximum pressing force: 300 kN
- Ram speed: 10 mm/s (manual operation), 50 mm/s (automatic operation)
- Working surface: 1200 x 700 mm
- Installation height: 750 mm
Application:
Universal tool testing and production press with high-precision stroke control and optional force control.
Hydraulic press (Hessmert)
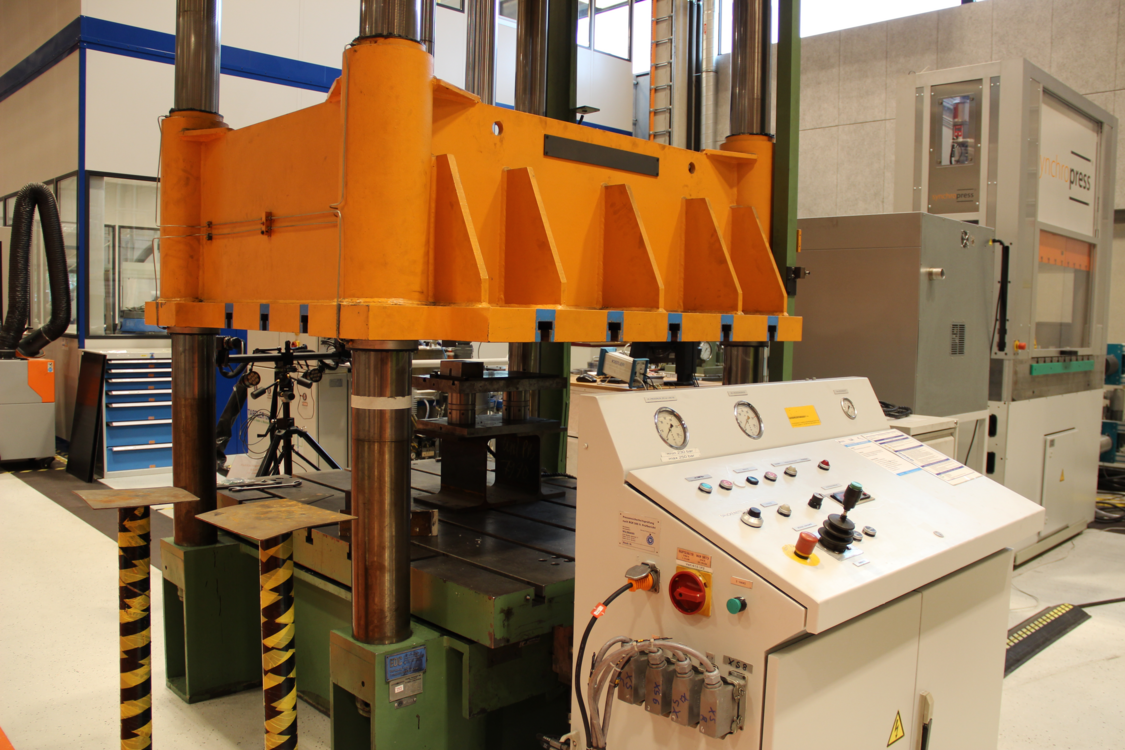
Technical specifications:
- Max. pressing force: 500 kN
- Max. Ram speed: 35 mm/s (upwards), 70 mm/s (downwards)
- Working surface: 1300 mm x 1800 mm
- Installation height: 1600 mm
Application:
All-purpose oil-hydraulic top ram press in column design for carrying out spotting work as well as for producing FKV and FKV-metal hybrid components, e.g. by means of resin injection processes.
We have machines to produce new, innovative and specialised metal powders in small batches for research and development.
The metal powder production field was rebuilt in 2020.
- AS 450 control vibrating sieve machine (Retsch)
- Air classifier AC1000G (Blue Power Casting Systems)
- Powder atomisation system AU 3000 (Blue Power Casting Systems)
- Tilting induction melting furnace IT-KTS-120/180/1900 (Linn High Therm)
- Vacuum quenching furnace XGraphit series (Xerion)
Contact person: Sven Gründer
Vibratory sieve shaker AS 450 control (Retsch)
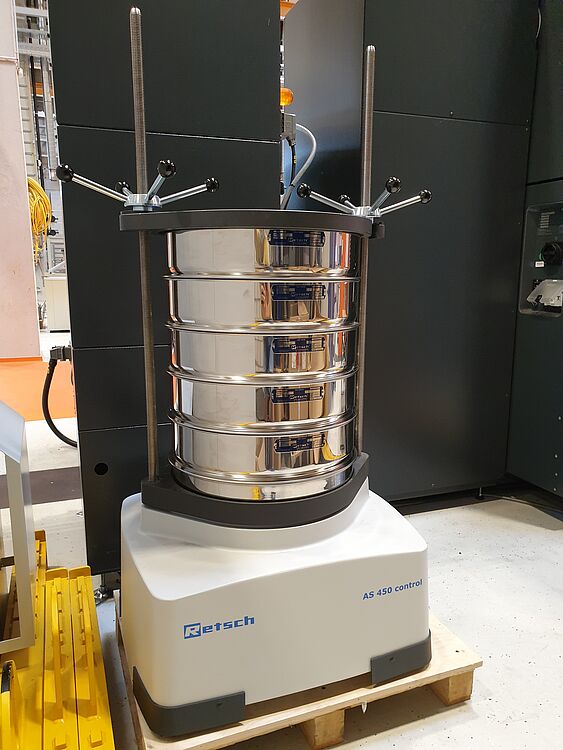
Technical specification
- Feed material: powders, bulk solids, suspensions
- Maximum quantity of material to be sieved: 25 kg
- Measuring range: 25 µm - 125 mm
- Maximum number of fractions: 13 / 9
- Minimum number of fractions: 3
- Amplitude: digital; 0.2 - 2.2 mm
- Sieving: dry and wet
Application
Separation, fractionation, particle size determination of powdery materials and bulk solids.
Air classifier AC1000G (Blue Power Casting Systems)
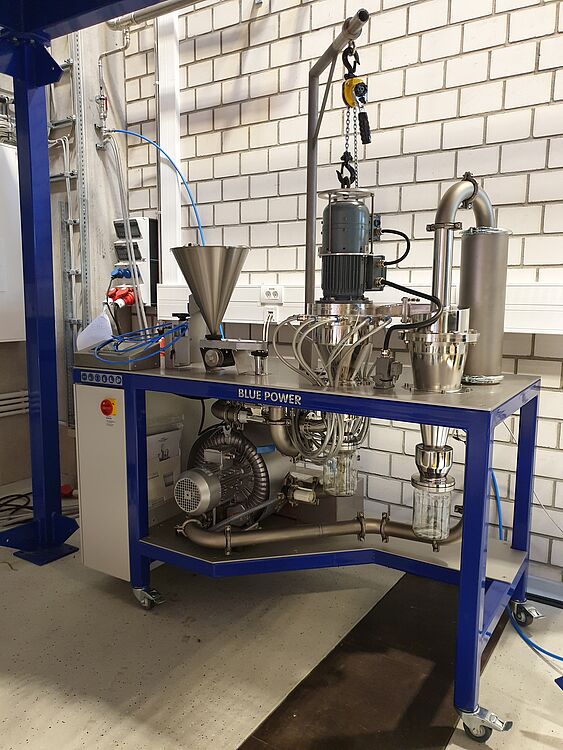
Technical specification
- Feed material: Powder
- Maximum feed quantity: 6 kg (bronze or steel)
- Classification range: 4 - 200 µm
- Protective atmosphere: argon or nitrogen
- Maximum speed of classifier wheel: 10000 min-1
Application
Flexible classification of powdery materials in small quantities. Separation of powder into fine and coarse powder fractions, especially in the field < 25 µm, where conventional screening methods usually fail.
AU 3000 powder atomisation system (Blue Power Casting Systems)
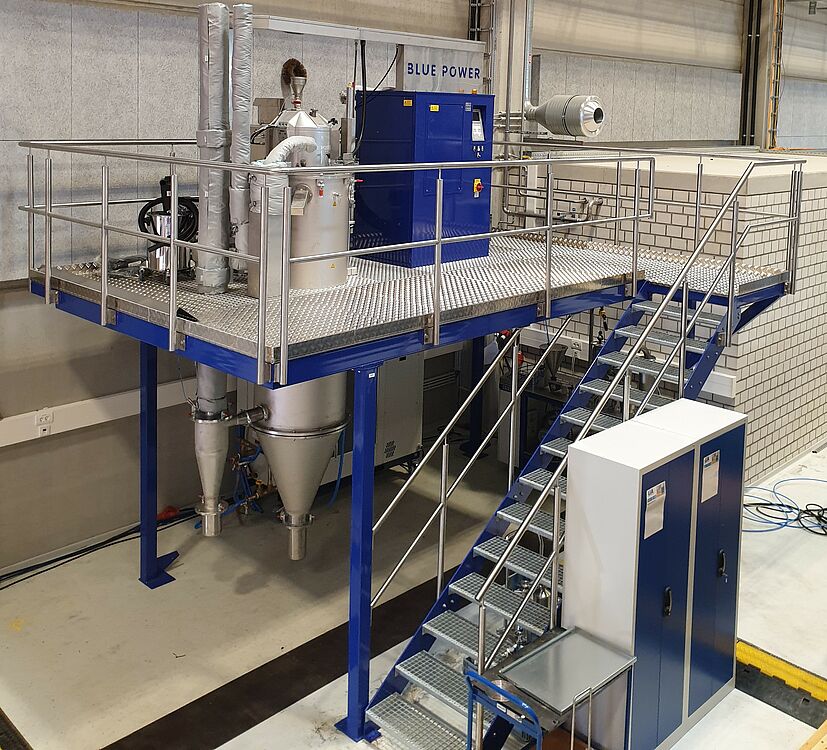
Technical specification
- Maximum temperature: 2000 °C
- Atomising medium: argon or nitrogen
- Maximum gas pressure: 30 bar
- Maximum gas temperature: 450 °C
- Atomiser nozzle system: free-fall and clouse-coupled atomiser
- Crucible volume: 3 l
- Maximum powder quantity (steel): 22 kg
- Cycle time: 3 - 4 h
Application
Production of new, innovative and specialised metal powders in small batches for research and development:
- Alloys that are not available on the market;
- Precious metals that are usually required in small quantities and where any metal loss must be avoided;
- Powder materials for additive manufacturing (powder-based processes: Laser/Electron-Beam Melting, Laser Metal Deposition) where high purity, sphericity and reproducible particle size distribution are required;
- Small-volume production with the lowest possible cross-contamination and short process time, which cannot be realised in an economically viable way on conventional systems.
We have several facilities that are used for quasi-static material testing of a wide variety of materials. One of these systems is, for example, the biaxial planar testing machine, which is used to perform multi-axis tensile tests in the plane to determine the isotropic and anisotropic material behaviour of various polymers.
- Servo-hydraulic testing machines up to 250 kN
Contact person: Marc-André Garthe
- High-temperature creep test rig
Contact person: Malte Dreyer
- Planar biaxial testing machine
Contact person: Dr. Barbara Floeing-Hering
Cupping test rig < 400° C
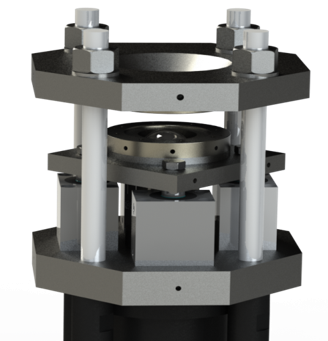
Technical specifications
- Nakajima punch Ø 100 mm
- Depth tests up to 400° C by heating punch and tools
- Various proven lubrication systems to minimise friction at different temperature ranges
- Maximum punch force up to 1000 kN
- Force recording up to 250 kN
- Displacement measuring system for recording the punch displacement
- Inline measurement of strain using optical measuring systems (gom ARAMIS)
Application
- Cupping tests according to DIN EN ISO 12004-2 to determine forming limit curves for different materials, sheet thicknesses and temperature ranges
Cryogenic test bench > 400° C
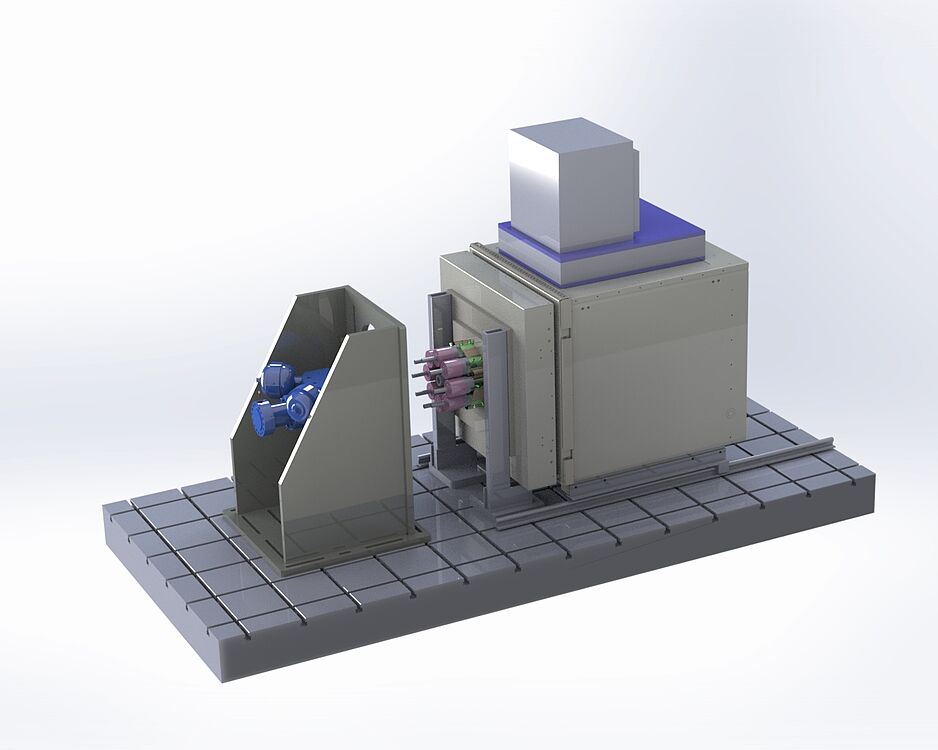
Technical specifications
- Nakajima stamp Ø 100 mm
- Cupping tests up to 800° C in isothermal furnace atmosphere
- Sluice system for sample feeding
- Maximum punch force up to 100 kN
- Force recording up to 100 kN
- Displacement measuring system for recording the displacement of the stamp
- Subsequent measurement of strain using optical measuring systems (gom ARGUS)
Application
- Cupping tests according to DIN EN ISO 12004-2 to determine forming limit curves for different materials, sheet thicknesses and temperature ranges
Planar biaxial testing machine
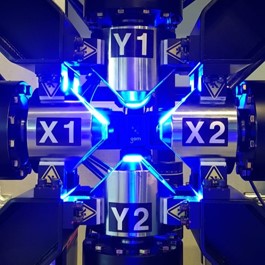
Technical specifications
-
4 actuators of two orthogonal load axes in one plane
-
Maximum forces per axis up to 25 kN
-
Force recording per axis up to 25 kN
-
Centre point control by actuator control
-
Displacement measuring system for recording the actuator movements
-
Determination of strains with optical measuring systems (gom ARAMIS)
Application
- Multi-axis tensile tests in the plane to determine the isotropic and anisotropic material behaviour of various polymers and fibre-reinforced plastics.
From classic manual machining to highly complex equipment, our trained workshop team is able to meet even the most complex workpiece machining requirements.
Contact person: Henrik Lenzmeier